How To Minimize Damage & Most Commonly Damaged Items During Shipping
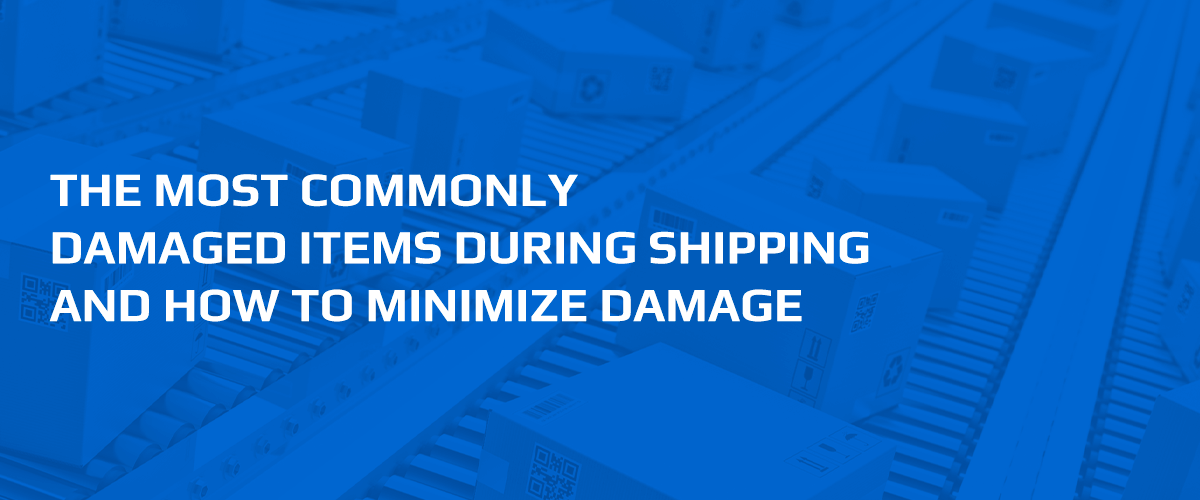
Posted: March 2022 Author: Jim Higgs
TABLE OF CONTENTS
Most Commonly Damaged Items
Most Common Causes of Shipping Damages
How to Prevent Shipping Damages
Are Carriers Liable for Shipping Damages?
Carriers occasionally damage shipments during transit as a result of human error. From dropping a package and causing the contents to shatter to crushing a box beneath a heavier package, some damage can be inevitable during shipping.
Whether you’re shipping items of high monetary value or fragile, one-of-a-kind mementos that hold sentimental value, it’s essential to protect your items during shipment with proper packaging. How do you ensure products aren’t lost or damaged during shipping? Use this guide to determine which items need the most protection and the best ways to package them to reduce the risk of damage.
Most Commonly Damaged Items
While all items are susceptible to damage during shipment, certain more fragile items break more frequently than others. To minimize damages to packages, you’ll want to take special care when packaging these items.
Here are the most commonly damaged items during shipping:
- Decorations
- Glassware
- Ceramics
- Electronics
- Jewelry
- Musical instruments
Most Common Causes of Shipping Damages
From packing methods to carrier practices and other uncontrollable external events, many factors can increase the chances of a damaged package during shipment. Here are the seven most common reasons for shipping damages:
- Empty space in packaging
- Poor choice of packing material
- Insufficient cushioning
- Improper handling
- Water and moisture exposure
- Insect or rodent damage
- Theft
How to Prevent Shipping Damages
Although many factors that influence shipping damages — like moisture levels or theft issues — are largely out of your hands, you can still lessen the risk of damaged shipments by properly packaging items. During shipments, packages must endure drops, compression from stacking boxes, rattling from conveyor belts and vehicles, temperature changes and more. Therefore, the proper packaging can make a difference.
Follow these shipping tips to avoid damage to your shipped items:
1. Buy New Packaging
While recycling an old box or mailer can help you save money on packaging and reduce unnecessary waste, it often poses a risk to your items. Used packaging has already been through the rigors of shipping at least once. As a result, some of its protective qualities may no longer function — the bubble packaging may have popped, or the corrugated cardboard could’ve collapsed during shipping.
It’s usually your best bet to purchase a new mailer to ensure your items stay as protected as possible. If you decide to reuse packaging, take special care to inspect it for damage. Any issues with structural integrity may lead to damaged products during shipment.
2. Use Sturdy Outer Materials
A package’s exterior is the first line of defense against shipping damages. Sturdy outer materials help protect your package from denting or collapsing under pressure, preventing shipping damage.
When shipping delicate items with a cardboard box, you should choose a box made with corrugated cardboard. Multiple layers of cardboard help the box maintain its structure, especially if the carrier stacks many other boxes on top of it.
For smaller items, padded mailers can offer similar protection. Though the package itself is relatively flexible, the padding cushions shipped items when someone drops it or it becomes crushed beneath other packages.
3. Select the Correct Packaging Size
The right packaging size can help to protect your shipped items while saving you money on shipping materials. If you choose a larger box than necessary, you’ll have to fill any open space with filler material to protect the items from bouncing around inside. The additional expense of void filler can add up over time.
If the packaging is too small for the items, the walls of the packaging will lose their structural integrity. Any cushioning materials will be under stress and may even break, which reduces the amount of protection the cushioning materials offer.
Always choose a package that fits your items securely inside without too much extra space.
4. Choose Packaging Based on Product
Keep in mind that different types of items require different types of packaging to prevent shipping damage. For example, clothing and other fabric items can easily handle bumps during transit, although they benefit from water-resistant retail packaging. On the other hand, when shipping delicate items like glassware, you should prioritize structural integrity and padding.
5. Use Special Packaging for Electronics
Specifically, electronics are highly susceptible to shipment conditions. Devices like televisions contain small, intricate components that can easily break or become dislodged under pressure. These objects are sensitive to moisture, and some components can become damaged or explode from electrostatic discharge (ESD).
Therefore, you should use a combination of packaging techniques depending on the item. Using anti-static material or other ESD packaging with another barrier material can help to protect your electronics from damage during shipment.
6. Wrap Every Item Individually
In addition to securing your package externally, you should protect your items from each other within the package. By wrapping items in cushioning materials, you can prevent them from knocking directly into each other during shipping, which helps avoid scratches and dents. For delicate items like ceramics, wrapping can prevent them from shattering.
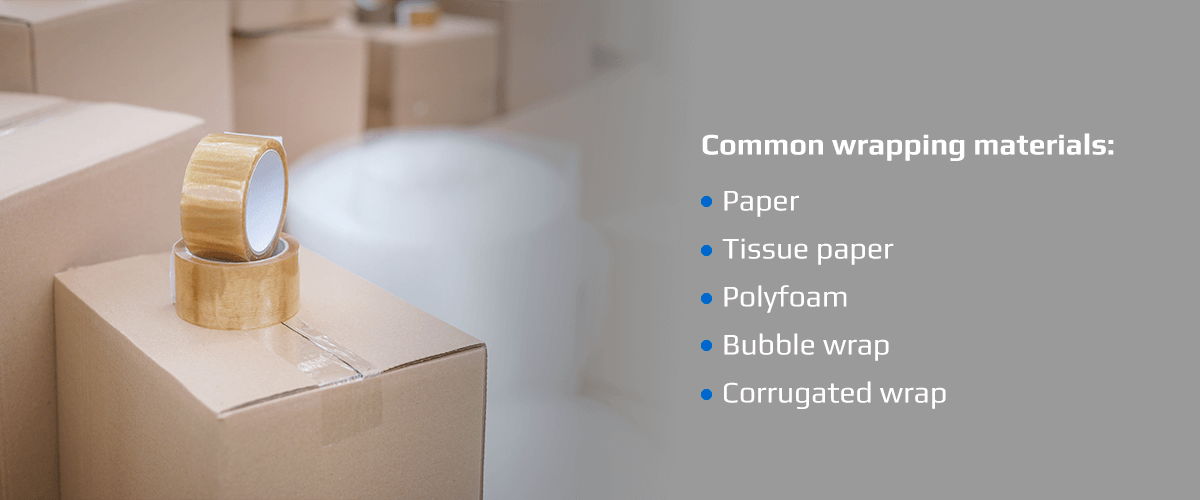
Here are some of the most common wrapping materials:
- Paper
- Tissue paper
- Polyfoam
- Bubble wrap
- Corrugated wrap
7. Fill Void Space
Although wrapping materials help fill out a package, any space in a box allows the items inside to bounce and shift during transit. If you shake a package and the objects rattle around inside, you should fill the void space with extra materials.
Here are some materials frequently used to fill void space:
- Packing peanuts
- Crumpled paper
- Air cushions
- Styrofoam
8. Properly Label Packages
By labeling your packages with handling instructions, you can inform carriers of the best way to handle the packages and avoid damages. For example, you can mark delicate packages with the words “Fragile” or “This Side Up” to show that carriers should take special care when moving the items.
Additionally, you can use handling indicators to show whether the carrier correctly handled the package during shipment for sensitive items. For example, tilt indicators can detect whether the carrier tilted a box and to what degree. Other indicator types include impact and shock indicators.
9. Pick the Right Packaging Material Supplier
The packaging material supplier you choose will depend on your needs and packaging standards. A reliable supplier should offer a wide selection of quality packaging materials at reasonable prices, and they should be able to consistently deliver products to you promptly to develop a constant workflow.
Are Carriers Liable for Shipping Damages?
When goods are damaged in transit, who is liable for the damages? Carriers in the United States are legally required to offer a liability program. However, carriers generally have the freedom to choose how much coverage to offer. Depending on the carrier and the types of items shipped, you may only receive a small percentage of your damaged shipment’s value.
Because carrier liability can only cover a small amount of your shipment’s value, it’s vital to focus on reducing product damage during shipping with quality packaging. Although it may be tempting to choose the least expensive packaging available, ultimately, you’ll lose more money from damaged items over time.
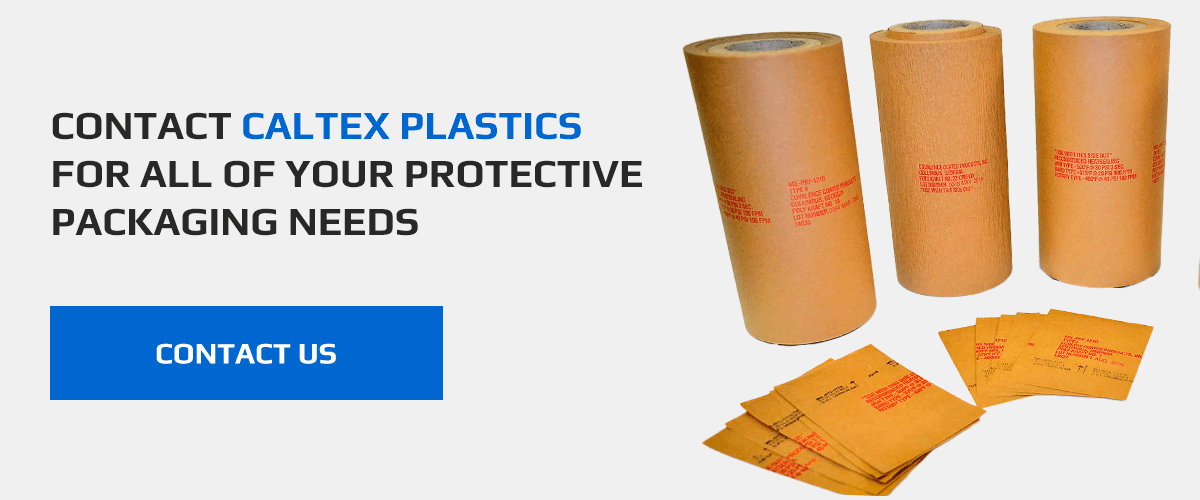
Contact Caltex Plastics for All of Your Protective Packaging Needs
When it comes to packaging items for delivery, it helps to have a reliable supplier with affordable packaging products. Caltex Plastics has provided customers with quality bags, tubing, pouches and more for more than 35 years. We strive to provide exemplary customer service and are available 24 hours a day, seven days a week, to meet your every need. If you’re ready to experience the Caltex difference, feel free to contact us today.